Research
Micro/Nanofabrication Processes
MEMS, with their multifunctionality and miniaturized forms, are increasingly
making unique contributions to a variety of application fields. They
however often encounter difficulties when interacting with external worlds
due to material incompatibility. This is largely attributed to the fact
that the range of materials available for conventional MEMS fabrication
is significantly limited. There are a vast range of high-performance
engineering materials as well as emerging nanomaterials that could be incorporated
in MEMS to advance their capability. This research focuses on bridging
the gap between diverse resource of non-traditional materials and MEMS
towards creating new application opportunities.
Metal Micromachining using Miniaturized Electrical Discharge
Micro-electro-discharge machining (µEDM) is a powerful and versatile micromachining technique as it
can be applied to any type of electrical conductors. The process thermally
etches a material using high-frequency pulses of micro arc discharge generated
between the material and the tip of cylindrical microelectrode. We are
investigating the physics of this discharge process and developing novel
µEDM methods. One focus has been on converting the mode of the process
from serial to parallel, by utilizing arrayed microelectrodes with distributed
power control. To this end, we developed microelectrode arrays through
lithographic processes and demonstrated batch-mode µEDM with high
parallelness using the arrays, showing >100x throughput improvement
compared with conventional µEDM methods. Along this line, we also demonstrated the first MEMS-based µEDM called
M3EDM, in which arrays of electrostatic actuators were created on the sample surface to drive microelectrodes for µEDMing. This approach provides a unique solution to high-throughput micropatterning of extremely large-area samples.
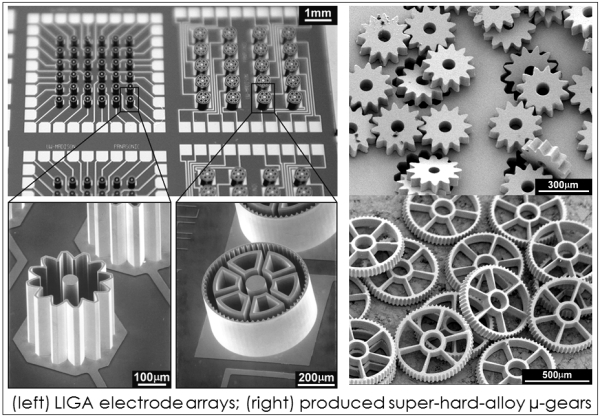
Micropatterning of Conducting Polymer
Polypyrrole and other conducting polymers are of interest in actuators,
sensors, energy storage devices, and organic electronics. The patterning
of these polymers in both macro and micro domains can be challenging, particularly
polypyrrole due to its insolubility. We showed the first micropatterning
of polypyrrole through a µEDM approach, by establishing high-frequency
pulses of miniaturized electrical discharge on the polymer. Microstructures
with surface roughness of 70 nm were produced with sub-micron depth control.
The process was used for electrical partitioning of polypyrrole film deposited
on a medical catheter, with a focus on the application to "smart"
catheters that use patterned polypyrrole as integrated actuators.
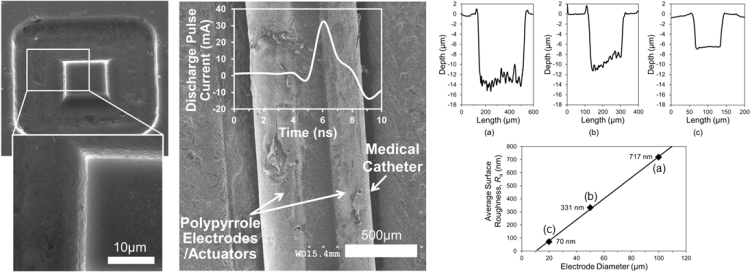
Post-Growth Micro/Nanopatterning of Carbon Nanotube Forest
This study involves the methods based on EDM as well as on mechanical manipulation
of the nanotubes. Refer to the Carbon Nanotube Forest section for details.
Microfabrication with Liquid Sacrificial Layer
We have developed a non-lithographic method to create suspended movable
diaphragms using the magnetic fluid called ferrofluid as a liquid-phase
sacrificial layer in the microfabrication process. Parylene C is directly
deposited on the ferrofluid sacrificial layer filled in a cavity in vacuum, forming a movable diaphragm suspended on the cavity after magnetically
removing the fluid using a permanent magnet. This approach enables extremely simple, fast, and low-cost production of capacitive
MEMS sensors while eliminating the need for photolithographic, bonding,
thermal, or chemical process. We demonstrated a stainless-steel-based capacitive
pressure sensor by leveraging this novel micromachining approach.

Lithography-Assisted Electroplating Bonding
Hybrid MEMS enabled by integration of micromachined functional bulk materials
is a promising path to achieving novel functionality and high performance
in the devices. Assembly of such microstructures often involves various
requirements including high bonding strength, electrical coupling, heat
transfer, and compatibility with planar microfabrication processes and
wafer-scale integration. We have developed an electroplating-based bonding
technique that fulfills these key features, This room-temperature process
enables assembly of bulk micromachined structures with microelectronic
circuits and other heat sensitive components with high bonding strength
and has been applied to the integration of shape-memory-alloy micro actuators
with their driving circuits.
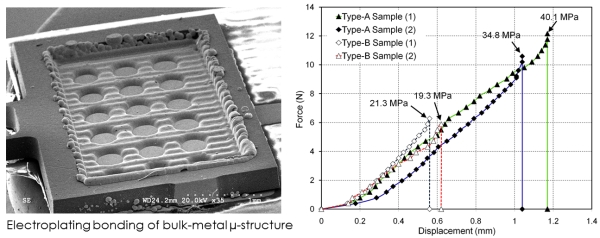
Laser Microwelding for MEMS Integration
Another approach to hybrid MEMS integration being investigated is laser microwelding. This process has
been shown to be very effective in bonding of stainless-steel-based MEMS
chips on metallic substrates or devices. The microwelded bond was found
to provide twice the mechanical strength and ~6x electrical conductance
compared with a conductive epoxy case. Microwelding of the stainless-steel
chip of capacitive pressure sensor was verified to preserve its sensing
performance. We demonstrated sensor integration on stainless-steel antenna stents using this approach toward "smart" stent application.

Jump to other research theme:
Micromachined Actuators
Micromachined Sensors
Medical MEMS
Carbon Nanotube Forest: Process and Application
The main page of Research

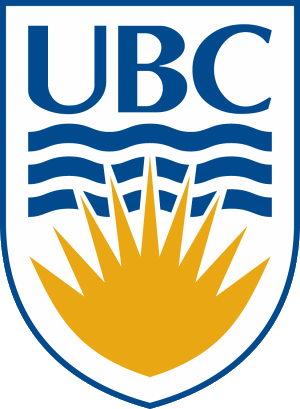